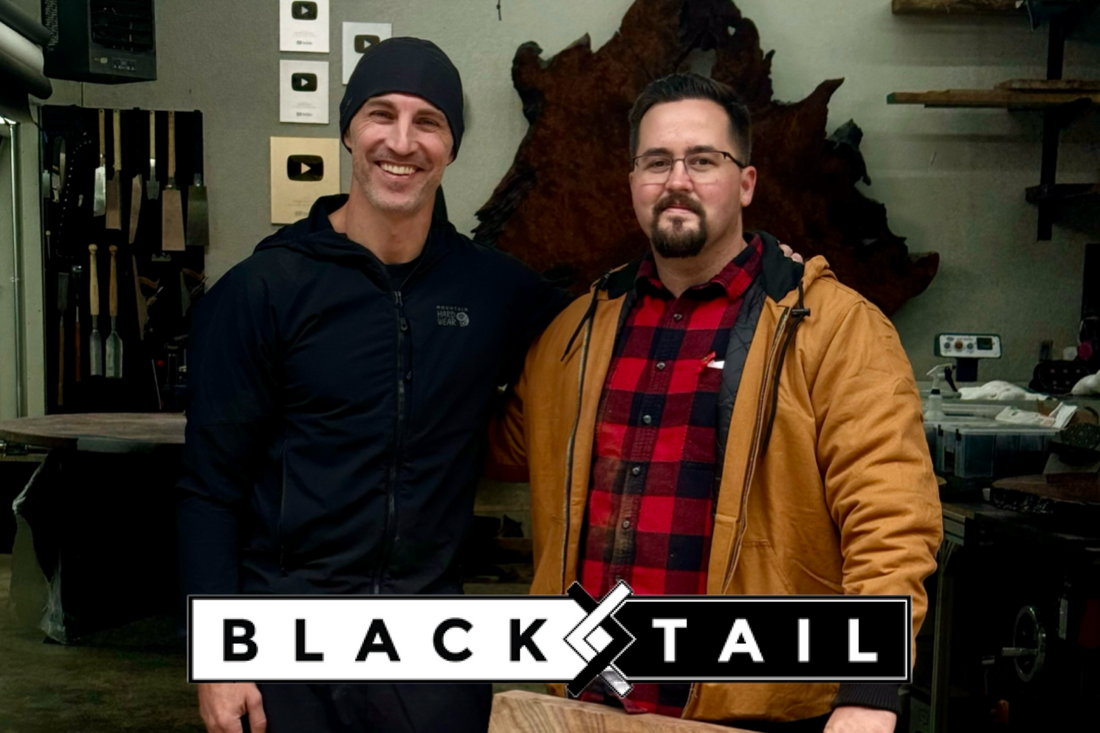
Blacktail Studio Guitars
Share
Blacktail Studio X The Wooden Hobbyist
Today, I have a wild tale that involves a road trip, a talented woodworker, and a hefty dose of walnut. Girthy, figured walnut from Blacktail Studio, to be exact.
It all started in the shop.
So, there I was, plotting my next big adventure in the world of guitar making. As I normally do, I just started milling wood while having YouTube playing in the background. At that time, I had a Blacktail Studio (Cam) build video going on and got the idea to make a guitar inspired by the video I was watching. Now, if you don’t know Cam, he’s like a rockstar of woodworking and epoxy furniture on YouTube. Seriously, his channel is a treasure trove of inspiration for anyone looking for some quality video's of quality woodworking. I reached out to him to see if he would be interested in some sort of collaboration and he actually responded. Which was insane. He offered up some huge cutoffs to use as guitar tops and invited us out to his shop.
My buddy Sean and I piled into the truck, fueled up on caffeine and excitement, and hit the road. It was a long drive, but we entertained ourselves with dad jokes and took turns driving. I’m pretty sure we scared a few passing motorists, but hey, it’s all part of the fun, right?
When we finally rolled up to Blacktail Studio, it didn't feel real. Cam welcomed us with open arms (and a mountain of walnut), and I immediately knew this trip was going to be legendary. It was cool to see some of the projects he was working on and to see the shop in person, a shop I've been watching him build things on YouTube for years. The only thing that would've been cooler than just being there, would be making some custom guitars there instead of driving it all the way home.


After a quick tour, it was time for the main event: the walnut. After messing with me by pretending to give me firewood, Cam gifted us some seriously impressive slabs, and I could already envision the guitars we were about to create. Specifically, he gave us some figured Bastogne Walnut and Claro Walnut Burl. Being from Missouri, I've never had the chance to work with wood this nice. Best part is, he gave us more than enough to make a few guitars with. The Bastogne Walnut, in particular, was from a pricey coffee table he built a while back and the figure was absolutely incredible.

He didn't stop there, either. On our way out the door, he gave us some offcuts from one of his denim tabs builds where he piled multiple layers of denim at epoxy. Little did I know, these tiny little denim scraps would take the project to a whole new level.
Starting on the builds.
Now, let’s talk about the magic of guitar making. If you’ve ever tried your hand at crafting a custom guitar, you know it can get a bit tricky. That’s where my trusty guitar making router templates come into play. I’ve designed these templates to make the process smoother than a well-polished fretboard. With my templates, even a first-timer can carve out a masterpiece without losing their sanity (or finger!).
Once we were back in Missouri, we wasted no time getting started. I personally wanted the builds to mimic Cam's designs with a focus on the walnut accompanied by black epoxy. Elegant and simple while letting Mother Nature do the hard work in the wood grain.

I'm not used to this type of wood for the type of woodworking I do. At least not the size of it. It felt like a lot of my tools were inadequate because my jigsaw couldn't even cut all the way through anything he gave us. Since the guitars were sort of an homage to Cam's furniture, I decided to book match the guitar tops and have a black epoxy river go down the center. It's important to note; I hate epoxy. Dearly. It's sticky, messy, toxic, and smells horrible, but the possibilities of the beauty it creates seem to outweigh the negative aspects.
For the body, I made my own guitar body blank out of strips of Birch and African Mahogany. I've always enjoyed mixing different species of wood to create color contrast and interesting designs. The reddish undertones of the African Mahogany also tied into the color the walnut brought out as well.
Shaping was simple with the templates, allowing me to focus more on the design details, like inlays. The inlays were a perfect area to incorporate the denim Cam provided. Instead of cutting, I decided to shave the denim with a rasp to create a blueish filler mixed with thin ca glue inside of a brass ring. It honestly turned out way better than expected and really popped from the mun ebony fretboard.

The Knobs...
Working through this build had me thinking about how custom something could truly be. I could've stopped early and just added finish then purchase some basic knobs, but, that couldn't be the case here. It was way more important to make them myself. I stacked some walnut, thin brass sheet, and denim to turn little Blacktail Studio knobs. In my opinion, and in the opinion of the tens of thousands of commenters across social platforms, these knobs were the best part of the build.
Finish
Final step was to add finish and hardware. I'd normally grain fill the guitar bodies with epoxy to give it a smooth, glass-like surface before applying finish. But, in the spirit of Blacktail Studio, I used a couple coats of Rubio Monocoat. Needless to say, the grain really popped. I've never worked with wood this beautiful before and I'm definitely taking another trip to Oregon to grab more sometime.
As we cut, shaped, and assembled our guitars, I couldn’t help but think about how exciting it is to blend woodworking with music. There’s something magical about taking a raw piece of wood and transforming it into an instrument that can create beautiful sounds. And now, thanks to Cam’s generosity, we were able to share that joy with others through our charity initiative. This trip was a whirlwind of creativity, laughter, and a newfound appreciation for the art of woodworking.
So, if you’re into guitar making, custom guitars, or woodworking, I invite you to join me on this journey. And don’t forget to check out my guitar making router templates – they might just save you from a woodworking disaster! Now, if you’ll excuse me, I have some walnut to sand and some dad jokes to perfect. Until next time, keep strumming and crafting!
If you'd like to see how this went down first hand, check out the video below.